How Robotics is Revolutionizing Power Infrastructure
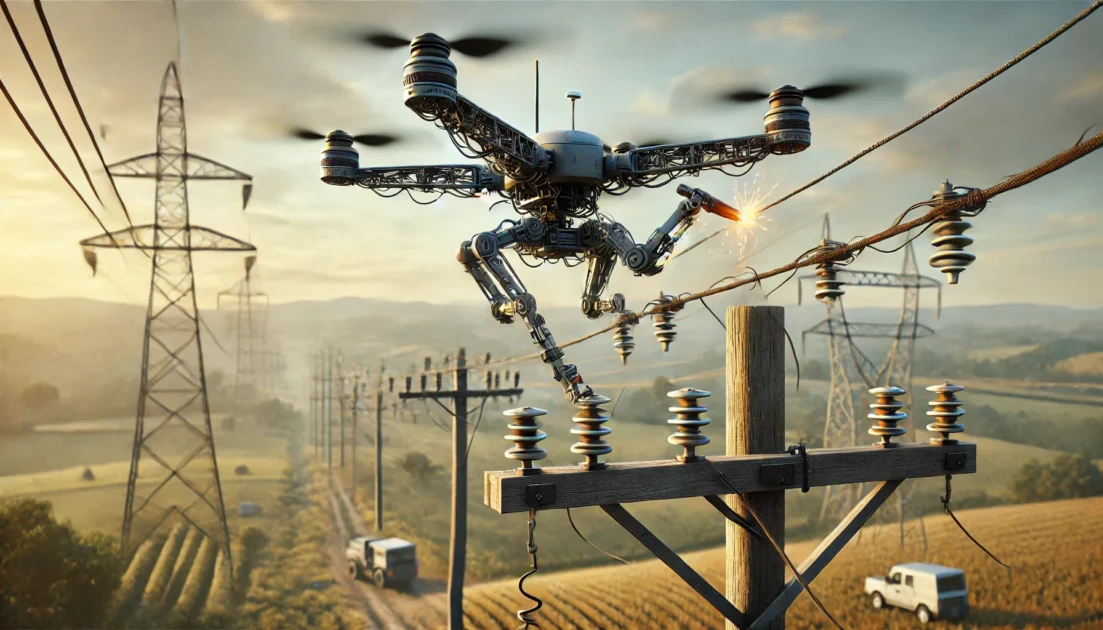
Robots are transforming the power sector by making operations safer, faster, and more efficient. Integrating advanced technologies such as drones, AI, and autonomous robots is revolutionizing how infrastructure is maintained and repaired. According to a MarketsandMarkets report, the global utility drone market is expected to grow from USD 150 million in 2020 to USD 630 million by 2025. The increasing use of robots for grid inspections, repairs, and vegetation management, allows faster data collection and more effective maintenance while reducing operational costs and risks.
Safer High-Voltage Line Repairs: Traditionally, lines were de-energized to allow workers to manually perform repairs which caused downtime and involved the risk of electrocution. However, modern robots, like the LineRanger from Hydro-Québec, are now designed to perform live-line maintenance. This robot navigates along power lines, using insulation technology to repair conductor damage without shutting off power, reducing risks for workers and maintaining service continuity.
Efficient Grid Inspections via Drones: Utility companies like Southern California Edison and National Grid in the UK have adopted drone technology for faster and more accurate inspections. Drones such as the DJI Matrice 300 RTK are equipped with high-definition cameras, LIDAR, and thermal imaging to inspect transmission lines, substations, and transformers which can detect issues like loose fittings, corrosion, or hotspots that might indicate overheating. In the past, inspections required expensive helicopters and time-consuming manual climbers. Drones now cover large areas more efficiently and at a lower cost. After California’s wildfires in 2020, Pacific Gas and Electric Company (PG&E) used drones to assess power line damage, helping restore power faster.
Substation Monitoring with Autonomous Robots: Substations, where voltage levels are adjusted for distribution, are critical components of the power grid and require constant monitoring. Robots like ANYmal are being deployed in substations to monitor electrical equipment autonomously. These robots are equipped with thermal sensors, infrared cameras, and gas detectors to continuously assess conditions, identifying problems such as overheating transformers or gas leaks. In Switzerland, Swissgrid has piloted ANYmal for 24/7 substation monitoring, reducing the need for manual inspections and increasing system reliability by detecting issues in real time.
Automated Cable Laying and Maintenance: Underground cable installation and maintenance are labour-intensive, especially in congested urban areas. Robotic trenching systems like TRACTO have automated cable laying by using trenchless technology, which digs and installs cables without needing to excavate large areas. This minimizes disruption to existing infrastructure. In London, where space is limited, TRACTO robots allow for quick and accurate installation, reducing costs and preventing traffic interruptions. Underground inspection robots, like Envirosight’s ROVVER X, can inspect and repair faults in underground cables, detecting issues like insulation degradation and preventing failures before they occur.
Vegetation Management with Drones: Vegetation encroachment is one of the leading causes of power outages, especially during extreme weather events. Traditionally, crews had to be deployed to physically inspect and trim vegetation near power lines. However, companies like PG&E now use drones and robotic cutters to manage vegetation proactively. These drones map vegetation growth through LIDAR and thermal sensors, allowing for precise trimming. In Florida, Duke Energy deployed similar drone technology after hurricanes to rapidly assess tree damage to power lines, restoring power in record time.
Disaster Recovery and Response: In the aftermath of storms, wildfires, or earthquakes, autonomous robots and drones can be sent into disaster zones to inspect power infrastructure safely and efficiently. Boston Dynamics’ Spot robot was deployed in Puerto Rico after Hurricane Maria to inspect damaged power lines and poles, gathering critical data in areas inaccessible to human workers. Robots like Spot are equipped with advanced cameras and sensors, providing real-time data that helps crews plan repairs more effectively.
AI-Powered Predictive Maintenance: AI-powered robots like Spot and ANYbotics collect massive amounts of operational data from equipment like turbines, transformers, and circuit breakers. This data is analyzed in real time, allowing AI models to predict when equipment might fail. For example, robots deployed at EDF’s nuclear power plants scan reactor components, identifying tiny anomalies that indicate wear and tear. By predicting failures before they happen, robots help avoid costly outages and extend the life of infrastructure.
The use of robots in the power sector is rapidly growing. National Grid in the UK is investing over GBP 16 million in robotic technologies for grid inspection and maintenance to reduce outages by 30% by 2030. In the U.S., Southern California Edison reports that drones have reduced the time required to inspect transmission lines by over 50%, providing faster fault detection and recovery. As robotics and AI technologies evolve, we can expect even greater advancements, ensuring that power grids worldwide become safer, smarter, and more resilient.
– Shivani Singh
AI can revolutionize power sector, however, it would interesting to see how it will affect job market in this industry.